
LEARN MORE
LEARN MORE
LEARN MORE
LEARN MORE
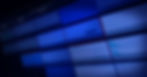
At SQUEAKS we provide manufacturing software
products and platforms for global manufacturing companies and industrial OEMs.
Our software products assist our customers in
achieving strategic business objectives for production efficiency, quality improvement, cost reduction, process control, along with team messaging and collaboration.
SQUEAKS gives you the power to personalizes the information your receive, making it easy to find the answers you want. With SQUEAKS, you receive only the information that is important to you!
Trust us with your communication platform like many other well-known companies have.
SQUEAKS is located in Louisville, Kentucky.
LEARN MORE
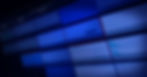
At SQUEAKS we provide manufacturing software
products and platforms for global manufacturing companies and industrial OEMs.
Our software products assist our customers in
achieving strategic business objectives for production efficiency, quality improvement, cost reduction, process control, along with team messaging and collaboration.
SQUEAKS gives you the power to personalizes the information your receive, making it easy to find the answers you want. With SQUEAKS, you receive only the information that is important to you!
Trust us with your communication platform like many other well-known companies have.
SQUEAKS is located in Louisville, Kentucky.
LEARN MORE
LEARN MORE
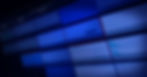
At SQUEAKS we provide manufacturing software
products and platforms for global manufacturing companies and industrial OEMs.
Our software products assist our customers in
achieving strategic business objectives for production efficiency, quality improvement, cost reduction, process control, along with team messaging and collaboration.
SQUEAKS gives you the power to personalizes the information your receive, making it easy to find the answers you want. With SQUEAKS, you receive only the information that is important to you!
Trust us with your communication platform like many other well-known companies have.
SQUEAKS is located in Louisville, Kentucky.
LEARN MORE
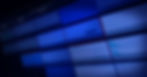
At SQUEAKS we provide manufacturing software
products and platforms for global manufacturing companies and industrial OEMs.
Our software products assist our customers in
achieving strategic business objectives for production efficiency, quality improvement, cost reduction, process control, along with team messaging and collaboration.
SQUEAKS gives you the power to personalizes the information your receive, making it easy to find the answers you want. With SQUEAKS, you receive only the information that is important to you!
Trust us with your communication platform like many other well-known companies have.
SQUEAKS is located in Louisville, Kentucky.
LEARN MORE
LEARN MORE
LEARN MORE
LEARN MORE
Search Results
Results found for ""
- IGear, LLC | Squeaks Software | 8016 Vine Crest Avenue, Louisville, KY, USA
Information Powered Best-in-class manufacturers rely on IGear software to drive mission-critical production applications – and optimize employee productivity. Closing the Gap IGear closes the gap between ... Information Technologies (IT) and Operational Technologies (OT) Office Workers and Frontline Workers ... to automate complex manufacturing processes and empower decision-makers. Platforms CONNECT - Data Service Platform CONNECT is a manufacturing data service platform that provides ETL/ELT capabilities among a diverse set of technologies to include factory floor devices, applications, and data structures to enable on-prem solutions and a “pipe” between the factory floor and the cloud. CONNECT leverages open standard and native protocols to enable both the control of a process in a mission critical capacity as well as the movement of data between systems in real-time or batch. CONNECT can run on-prem, hybrid (Edge), or in the cloud depending on application requirements and has become a standard platform among leading companies due to its proven track record for reliability, fault tolerance, and flexibility for more than 20 years. SQUEAKS - Productivity Platform SQUEAKS is a visualization and action management platform for everything that happens on the factory floor. When critical events and negative data trends occur, SQUEAKS kicks-in with 1) targeted alerts that include workflows and escalation rules that cannot be ignored, 2) real-time metrics and dashboards broadcast across digital signage displays throughout the plant, and 3) interactive One-Source boards on the plant floor that enable collaboration to quickly solve problems and advance continuous improvement activities. With SQUEAKS running as an app in Microsoft Teams, everything that happens in SQUEAKS is now seamlessly integrated with Microsoft Teams, converging OT and IT networks by extending Teams to the plant floor while improving collaboration and communication between office workers and frontline workers. MES Solutions ASSIST - Product Traceability & Process Interlocking ASSIST is IGear’s solution for contextualizing real-time, serialized manufacturing data to include individual products, consumed components, cycle anomalies, associated process data, defect tracking, and operator information. The result is a digital, on-demand traceability and genealogy birth certificate for each product. ASSIST can interface with every control system and machine in the process to validate and control the flow of good products from machine-to-machine, while preventing non-conforming products from leaving the plant. When ASSIST is fully implemented, individually serialized products associated with operator mistakes and/or machine failures will not be cleared for shipment to the end customer. ASSIST integrates with ERP systems to automate the broadcast of production schedules, bill-of-material information, and part/recipe specifications to the factory floor while also providing real-time inventory status information back to the ERP system. SQUEAKS PI - Production Intelligence SQUEAKS PI (Production Intelligence) is IGear’s solution for measuring manufacturing performance and contextualizing manufacturing data by work center, product type, production day, shift, machine fault, root cause, and more. With real-time machine connectivity, data is aggregated at various levels of granularity and is published to SQUEAKS in the form of metrics and datasets to be used in SQUEAKS dashboards in an off-the-shelf manner. Additionally, SQUEAKS PI provides configurable business rules to trigger squeaks messages based on machine data and events in real-time, providing an off-the-shelf data source for escalating alerts and workflows through the SQUEAKS platform. SQUEAKS PI needs only a single part count input to calculate accurate manufacturing performance to include cycle time, downtime, and OEE. IGear Complem ents The T ools You Already Use. IGear gets the most out of the best-in-class technologies and tools you already have in-place. We embrace open standards and native protocols to leverage your current technology investments and keep your costs low. Microsoft Partnership IGear complements Microsoft products to accelerate innovation, optimize operations, empower workers, and enhance customer satisfaction. Microsoft Teams Microsoft 365 Microsoft Azure Open AI Teams + IGear Running as an app within Teams, SQUEAKS provides real-time, plant floor visibility into what’s important now – escalating critical alerts from machines and drops in performance to ensure nothing important is going to slip through the cracks. Azure + IGear CONNECT provides an information pipeline between the technologies and systems on the shop floor to Azure – unlocking valuable data, with context, for cloud-based analytics tools and business applications to take advantage of. Open AI + IGear Given today’s labor market, IGear software helps manufacturers leverage the latest in information technology tools such as AI to innovate and solve problems faster with less resources. Ignition + IGear After a concerning event is made visible on the Ignition screen, SQUEAKS directs it to the right person in a targeted fashion with workflows that provide guidance and escalation rules that create a greater sense of urgency. IGear recognizes the importance of timely information in the hands of the right people. In manufacturing, any number of events can cause a machine to drop out of automatic or a key performance metric to fall short of the goal. Highlighting where action is required is critical given the importance of uptime, product quality, customer satisfaction and employee safety. IGear improves production efficiency and increases profitability by ... Driving action and extending visibility of critical events and KPIs Moving data between technologies for real-time process control Contextualizing data and events for cloud applications AI enablement
- Escalating Alerts | igear
Escalating Alerts Some Alerts Cannot Be Ignored. At IGear, we have decades of experience in manufacturing. We understand the cost of downtime, we know how hard it is to find people, we know that means your team members need to cover more ground – and get more done with less. We know everyone on your team comes to work every day wanting to do a good job and build a good product, but things (events) often get in the way. These events, or what we call a Squeak, can include a piece of equipment dropping out of automatic, a key performance metric dropping below target, or someone at the line calling for help, to cite a few. These events happen every day, every shift, every hour. When they happen, the logical question then becomes ... “Now what?” . Drives Action A Squeak can be automatically generated by a machine or database field, ... SQUEAKS is founded on proven manufacturing principles including the elimination of all waste in the pursuit of the most efficient methods and most productive workers. We start by drawing attention to the concerning event. SQUEAKS provides real-time, at-a-glance feedback – with a modern, digital twist – cutting response times from minutes to seconds. Personalized ... or manually by a team member via an operator station, or the SQUEAKS app. SQUEAKS is personalized. With SQUEAKS, you tune into what matters to you based on your responsibilities – minimizing distractions. SQUEAKS sends you only the information you need, when you need it, wherever you are. Unlike traditional systems (stack lights, ANDON boards, HMIs, radios, etc.) that communicate limited amounts of information in more of a broadcast, noisy and open-loop manner; notifications from SQUEAKS are rich in content, targeted and closed-loop. SQUEAKS messages demand attention – they cannot be ignored. Workflows Workflows reduce the time to resolve a problem by providing guidance, work instructions, and supporting documents, etc. Workflow actions can be triggered and closed out manually by authorized personnel or automatically by the machine/controller itself – it’s up to you. SQUEAKS seamlessly integrates with other applications. Events and associated Workflows can be initiated by other applications via SQUEAKS APIs and easily incorporated into a SQUEAKS message. The SQUEAKS escalation process and rules provide a framework for ensuring that concerning events (downtime, product quality, operator calls, etc.) are addressed at the appropriate level of management based on their severity and complexity. An escalation process can also be initiated if a Squeak isn’t acted upon in a timely or correct manner. Escalation Process You decide how and when you want the escalated alert to move up the chain of command and how you want to be notified. In many organizations, the process includes a set of predefined escalation levels, each corresponding to a different level of management responsibility depending on the condition/event. For example, a Level 1 issue may be addressed by a team leader, while a Level 2 issue may be escalated to a department manager or area leader. More complex or critical issues may be escalated to higher levels of management, up to and including the executive leadership team. The escalation process helps ensure that “issues or events” are addressed promptly and effectively and that the appropriate resources are allocated to resolve the issue. By escalating issues as needed, teams can quickly access the expertise and resources they need to identify the root cause of the problem and implement an effective correction action plan. 1/6 Extends Visibility Following a concerning event, SQUEAKS focuses on what’s important now (WIN). Our goal is to help you and everyone around you achieve more and stress less. More often than not, you are already capturing the concerning event in your PLC, HMI, or database. SQUEAKS taps into your existing system and unlocks the valuable information – communicating it to the right people wherever they are – and ensuring it is acted upon. Unlike traditional plant communication systems that require you to be within line of sight of the stack light, HMI, or Andon Board; SQUEAKS extends visibility to mobile devices and smart watches. SQUEAKS runs on all your communication devices. In addition to extending visibility, SQUEAKS provides greater insight by incorporating richer, more meaningful content. Whereas stacklights, HMIs and Andon Boards often communicate in Morse code, SQUEAKS can attach photos, videos, and documents that enhance communication and facilitate a quicker resolution. SQUEAKS drives accountability. From “Got It” to “Complete”, SQUEAKS maintains a digital trail of every action taken throughout the problem-solving process – creating a greater sense of urgency while giving you the confidence that everything is covered. After-the-fact, SQUEAKS provides reports that allow you to analyze what happened, how often, who was involved, and how long each step in the process took to complete. SQUEAKS enables an unprecedented level of countermeasures and continuous improvement leveraging factual information rather than guesswork. Microsoft Teams Integration Everything you can do with SQUEAKS can now be done from Microsoft Teams. If you are a manager and you use the Teams platform for communication, SQUEAKS can deliver real-time machine/process alerts and production reports directly to you in the Teams platform allowing managers and front-line workers to collaborate like never before.
- Escalating Alerts | igear
Escalating Alerts Some Alerts Cannot Be Ignored. At IGear, we have decades of experience in manufacturing. We understand the cost of downtime, we know how hard it is to find people, we know that means your team members need to cover more ground – and get more done with less. We know everyone on your team comes to work every day wanting to do a good job and build a good product, but things (events) often get in the way. These events, or what we call a Squeak, can include a piece of equipment dropping out of automatic, a key performance metric dropping below target, or someone at the line calling for help, to cite a few. These events happen every day, every shift, every hour. When they happen, the logical question then becomes ... “Now what?” . Drives Action A Squeak can be automatically generated by a machine or database field, ... SQUEAKS is founded on proven manufacturing principles including the elimination of all waste in the pursuit of the most efficient methods and most productive workers. We start by drawing attention to the concerning event. SQUEAKS provides real-time, at-a-glance feedback – with a modern, digital twist – cutting response times from minutes to seconds. Personalized ... or manually by a team member via an operator station, or the SQUEAKS app. SQUEAKS is personalized. With SQUEAKS, you tune into what matters to you based on your responsibilities – minimizing distractions. SQUEAKS sends you only the information you need, when you need it, wherever you are. Unlike traditional systems (stack lights, ANDON boards, HMIs, radios, etc.) that communicate limited amounts of information in more of a broadcast, noisy and open-loop manner; notifications from SQUEAKS are rich in content, targeted and closed-loop. SQUEAKS messages demand attention – they cannot be ignored. Workflows Workflows reduce the time to resolve a problem by providing guidance, work instructions, and supporting documents, etc. Workflow actions can be triggered and closed out manually by authorized personnel or automatically by the machine/controller itself – it’s up to you. SQUEAKS seamlessly integrates with other applications. Events and associated Workflows can be initiated by other applications via SQUEAKS APIs and easily incorporated into a SQUEAKS message. The SQUEAKS escalation process and rules provide a framework for ensuring that concerning events (downtime, product quality, operator calls, etc.) are addressed at the appropriate level of management based on their severity and complexity. An escalation process can also be initiated if a Squeak isn’t acted upon in a timely or correct manner. Escalation Process You decide how and when you want the escalated alert to move up the chain of command and how you want to be notified. In many organizations, the process includes a set of predefined escalation levels, each corresponding to a different level of management responsibility depending on the condition/event. For example, a Level 1 issue may be addressed by a team leader, while a Level 2 issue may be escalated to a department manager or area leader. More complex or critical issues may be escalated to higher levels of management, up to and including the executive leadership team. The escalation process helps ensure that “issues or events” are addressed promptly and effectively and that the appropriate resources are allocated to resolve the issue. By escalating issues as needed, teams can quickly access the expertise and resources they need to identify the root cause of the problem and implement an effective correction action plan. Desktop Screenshots Manual Call For Initial Downtime Alert SQUEAK Claimed SQUEAK Escalated Quality Team is Requested SQUEAK Completed History Becky.TeamMember Calls for Component Concern – State: Line Down Sandy.TeamLeader Claims the SQUEAK – State: Working on it The SQUEAK has been in the “Working on it” state for longer than one minute and is escalated. Managers are notified – State: Working on it escalated Sandy.TeamLeader Requests assistance from the quality team by notifying Mark.LineLeader – State: Working on it escalated Mark.LineLeader completes the SQUEAK – State: Back to Running Digital trail of the downtime event Desktop Screenshots Machine Call For Initial Downtime Alert SQUEAK Claimed SQUEAK Escalated Quality Team is Requested SQUEAK Completed History The MES System at Line 1 detects a Downtime Concern and automatically Calls for Component Concern – State: Line Down Sandy.TeamLeader Claims the SQUEAK – State: Working on it The SQUEAK has been in the “Working on it” state for longer than one minute and is escalated. Managers are notified – State: Working on it ESCALATED Sandy.TeamLeader Requests assistance from the quality team by notifying Mark.LineLeader – State: Working on it ESCALATED Mark.LineLeader completes the SQUEAK – State: Back to Running Digital trail of the downtime event Mobile Device Screenshots Manual Call For Initial Downtime Alert SQUEAK Claimed SQUEAK Escalated Quality Team is Requested SQUEAK Completed History Becky.TeamMember Calls for Component Concern – State: Line Down Sandy.TeamLeader Claims the SQUEAK – State: Working on it The SQUEAK has been in the “Working on it” state for longer than one minute and is escalated. Managers are notified – State: Working on it ESCALATED Sandy.TeamLeader Requests assistance from the quality team by notifying Mark.LineLeader – State: Working on it ESCALATED Mark.LineLeader completes the SQUEAK – State: Back to Running Digital trail of the downtime event Mobile Device Screenshots Machine Call For Initial Downtime Alert SQUEAK Claimed SQUEAK Escalated Quality Team is Requested SQUEAK Completed History The MES System at Line 1 detects a Downtime Concern and automatically Calls for Component Concern – State: Line Down Sandy.TeamLeader Claims the SQUEAK – State: Working on it The SQUEAK has been in the “Working on it” state for longer than one minute and is escalated. Managers are notified – State: Working on it ESCALATED Sandy.TeamLeader Requests assistance from the quality team by notifying Mark.LineLeader – State: Working on it ESCALATED Mark.LineLeader completes the SQUEAK – State: Back to Running Digital trail of the downtime event Extends Visibility Following a concerning event, SQUEAKS focuses on what’s important now (WIN). Our goal is to help you and everyone around you achieve more and stress less. More often than not, you are already capturing the concerning event in your PLC, HMI, or database. SQUEAKS taps into your existing system and unlocks the valuable information – communicating it to the right people wherever they are – and ensuring it is acted upon. Unlike traditional plant communication systems that require you to be within line of sight of the stack light, HMI, or Andon Board; SQUEAKS extends visibility to mobile devices and smart watches. SQUEAKS runs on all your communication devices. In addition to extending visibility, SQUEAKS provides greater insight by incorporating richer, more meaningful content. Whereas stacklights, HMIs and Andon Boards often communicate in Morse code, SQUEAKS can attach photos, videos, and documents that enhance communication and facilitate a quicker resolution. SQUEAKS drives accountability. From “Got It” to “Complete”, SQUEAKS maintains a digital trail of every action taken throughout the problem-solving process – creating a greater sense of urgency while giving you the confidence that everything is covered. After-the-fact, SQUEAKS provides reports that allow you to analyze what happened, how often, who was involved, and how long each step in the process took to complete. SQUEAKS enables an unprecedented level of countermeasures and continuous improvement leveraging factual information rather than guesswork. Microsoft Teams Integration Everything you can do with SQUEAKS can now be done from Microsoft Teams. If you are a manager and you use the Teams platform for communication, SQUEAKS can deliver real-time machine/process alerts and production reports directly to you in the Teams platform allowing managers and front-line workers to collaborate like never before. Teams Mobile Device Screenshots Manual Call For Teams Mobile Device Screenshots Machine Call For The Call for Component Concern notification received on Microsoft Teams The machine-generated Component Concern notification received on Microsoft Teams
- LineSide Labeling | igear
Lineside Labeling Eliminates Labeling Errors For manufacturers, a mislabeled shipping container or a container with incorrect quantities is considered a serious defect that can lead to costly consequences. Human error is most often the culprit when label mistakes happen, which is why many industries require that labels are not batch printed but individually produced based on machine events at the point of production (i.e. lineside labeling). ASSIST™ provides a label Error proofing solution which is designed to satisfy core Minimum Process Requirements (MPRs) for lineside labeling by replacing the batch label printing process with a solution leveraging automated machine data collection to determine that the container being packed is labeled properly and contains the correct quantity. Additionally, the ASSIST™ system adapts to your current infrastructure, so there is no need to replace your current EDI software or upgrade your machine controls. The following illustration and list of capabilities highlights some of the key aspects of the ASSIST™ software product. Capabilities Overview Collects part type and part count data from various machines and devices to include PLCs, weigh scales, vision systems, leak tests, various serial and Ethernet devices, robots, machine tools, presses, I/O, and virtually any technology commonly found on the plant floor. Provides live feedback to the operator with respect to part number being packed, current quantity, and any system errors or faults. Seamlessly interfaces with a variety of ERP systems to effectively trigger the printing of each label. Allows operators or supervisors to intervene in the process by reprinting labels and manually adjusting part counts. Stores all events in a historical system audit log for traceability purposes, including the customer serial number for each label that has been printed. Provides and administrative interface for creating and editing part numbers, part type relationships, container quantity, users, groups, etc. Traceability Error Proofing Manufacturing Intelligence ERP Integration Lineside Labeling Operator Assistance
- Error Proof | igear
Error Proofing Improves Manufacturing Quality Through Process Error Proofing Successful manufacturers are driven to build high-quality products. Quality management and error proofing encompasses a broad range of concerns including: preventing defects from ever occurring, reducing product variation through tighter controls and improved communication, and ensuring proper components are used/labeled throughout the assembly process – all of which ensure each part is built to its design specifications, on-time, the first time. With ASSIST™, the benefits of six-sigma quality include increased customer satisfaction and loyalty, supplier/regulatory compliance, labor savings and improved asset utilization through the reduction of rework, and cost savings through the avoidance of complaints and warranty claims. Total quality management applies to nearly all assembly or fabrication scenarios and usually involves the integration of information from a myriad of dissimilar shop floor technologies and business software applications. Regardless of the challenge, IGear’s proven ASSIST™ software product ensures a zero defect manufacturing process. The following illustration and list of capabilities highlights some of the key aspects of the ASSIST™ software product. Download bill of materials and specification information from virtually any business system Import a sequence schedule in a variety of formats Receive and validate operator login using various devices and methods Isolate and manage quality issues and report non-compliance concerns Interface to equipment controls for process interlocking purposes Ensure correct materials and parts are used and assembled with precision and accuracy Empower team members on the production line to monitor and validate quality Contain defective parts and prevent them from shipping to the customer Validate that parts exit the line and are shipped in sequence per the build schedule Capabilities Overview Traceability Error Proofing Manufacturing Intelligence ERP Integration Lineside Labeling Operator Assistance
- Production Efficiency | igear
Production Efficiency Improve Production Efficiency - Today Do you want to save your company time and money while boosting production efficiency? Do you feel your communication channels aren’t working the way they should? Are you having trouble tracking your employees’ actions following concerning events, workflows or other aspects of your business? Talk to us about investing in SQUEAKS, our industry communication platform that provides an innovative solution to all of your communication issues. You can send messages in real time, collect the data you need without having to weed through data you don’t, and even send image files directly, so you can see what’s stopping production or what’s performing effectively. With SQUEAKS, your machines are part of the conversation. Contact us today at INFO@IGEAR.COM to learn more about SQUEAKS and all of the productive ways it can help keep your business running smoothly. We are excited to talk to you more; Check out the videos of our efficiency-enhancing program at SQUEAKS . REQUEST A DEMO SQDC Boards Software Manufacturing “Call For ...” Mobile Andon Organize & Share Videos Mobile App for Stack Lights Worker Productivity Software IoT Software Communication Platform Real-time Manufacturing Information Manufacturing Productivity Production Efficiency Manufacturing Execution Systems Production Displays Manufacturing Software App Floor Management Development Systems (FMDS) Transforming Visual Management Boards Visual Management Microsoft Power BI + Squeaks Manufacturing Communication
- Meet SQUEAKS | igear
MEET SQUEAKS In the high-stakes world of manufacturing, even the most efficiently run operations need a little help from time to time. Because staying ahead of interruptive events that impede progress is critical not only to your production line, but it’s also key to your bottom line. And that’s where this guy comes in. Meet SQUEAKS. The bright little sprite from IGear who takes his name from what he does. Anytime your line experiences an issue, a problem, or a need, anywhere in your production process, SQUEAKS speaks up! He’s on call 24/7 to keep an eye out for potential issues, and when he finds them, he immediately finds you and your team members wherever you are! You no longer need to remain in earshot or eyeline of your ANDON system because SQUEAKS is Smart. And always close at hand. He’s your Digital Assistant, your high-tech virtual Efficiency Expert who goes where you go, on your smartphone, tablet, or desktop. So, he’s never further away than your own hip pocket. And SQUEAKS is popular, too! He’s already on the job at some of the world’s leading manufacturers – helping to make their operations more efficient and, as a result, more productive. SQUEAKS, It’s his job to make your job easier. Get to know him. Put him to work for you. Because SQUEAKS knows that when it comes to ensuring profitability and securing success, productivity is everything.
- ERP | igear
ERP Integration Automates ERP and Shop Floor Integration The need to integrate information throughout the manufacturing enterprise is heightened by the pace of business. In order to maximize control of production operations, information must reliably flow between a variety of business applications and shop floor automation equipment. The real-time synchronization of shop floor data with ERP systems enables better decision making and operational agility. With ASSIST™, the automated, bi-directional flow of data enables manufacturers to optimize equipment utilization while at the same time more accurately update WIP inventory with what is physically produced on the shop floor. ERP systems broadcast critical build information to the shop floor in the form of production schedules, part/recipe programs, and work instructions. At the same time, business systems are updated with timely inventory usage, product genealogy, and order status. The benefits are improved inventory control, optimized asset utilization, enhanced lot tracking and scrap reporting, automated data collection and the proper labeling of parts. The following illustration and list of capabilities highlights some of the key aspects of the ASSIST™ software product. Capabilities Overview Automated transfer of product configuration and real-time production data Broadcast assembly information from virtually any ERP system including: schedules, part lists, bill of materials, recipes, and work instructions Interface to a diverse set of machine controls for detecting part type, production counts, downtime events, and capacity limitations Dynamically adjust schedules based on raw material and equipment availability Immediately notify key personnel and interlock the process in the event of corrupt data (unknown part number, production count decrementing or increasing dramatically, etc.) Manage ERP transactions (tighter inventory control, scrap reporting, lot tracking, etc.) without data loss using fault tolerant data transport Provide an administrator interface for configuring the system to include stations, screen layout, ERP transactions, bill of materials, work instructions, printers, users, user certification, security groups,shift schedules, and system parameters Report status of all machine interfaces, transaction queues, and work stations Enhanced decision making as accurate information gets to the right people in a timely manner Traceability Error Proofing Manufacturing Intelligence ERP Integration Lineside Labeling Operator Assistance
- Get Started Package | igear
GET STARTED PACKAGE Fill out this form and we will contact you to process payment and provide software download instructions. Business Email First Name Last Name Business Phone Organization Name Questions/Comments Send Thanks for submitting!
- Manfacturing Communication | igear
Manufacturing Communication Drive Results With Time-Sensitive Communication If you have trouble communicating with people across your factory or want to make sure your workers are acting promptly on concerning events, SQUEAKS is the perfect manufacturing communication platform for you. Thanks to the intelligent machines that you have in your plant, there is probably a vast amount of data constantly coming to you. Wouldn’t it be great to sort that data and have access only to what you need at that specific time? SQUEAKS is designed to provide you with insight and personalized information feeds. It promotes collaboration, so you can meet your business goals every day. It promotes teamwork, keeping everyone updated on the processes taking place in your plant. Engage your employees and improve the quality of your work environment while driving continuous improvement. To learn more, contact us at INFO@IGEAR.COM . We would be more than happy to explain how SQUEAKS can help you improve your communication in the workplace. REQUEST A DEMO SQDC Boards Software Manufacturing “Call For ...” Mobile Andon Organize & Share Videos Mobile App for Stack Lights Worker Productivity Software IoT Software Communication Platform Real-time Manufacturing Information Manufacturing Productivity Production Efficiency Manufacturing Execution Systems Production Displays Manufacturing Software App Floor Management Development Systems (FMDS) Transforming Visual Management Boards Visual Management Microsoft Power BI + Squeaks Manufacturing Communication